铝型材开模定制步骤--第一篇
作者:万原铝制品 日期:2025-02-19 来源:万原铝制品 关注:1
一共分为三个步骤,篇幅较长今天先给大家分享第一阶段——前期准备阶段
需求分析
用途和场景:明确定制铝型材是用于建筑结构、机械设备、电子产品外壳、装饰材料还是其他特定领域。例如,如果是用于建筑结构,需要考虑到其承载能力、耐候性等因素;若是电子产品外壳,则更注重外观的精美程度、散热性能等。
尺寸和形状:精确测量所需铝型材的尺寸,包括长度、宽度、高度、半径等。对于形状复杂的型材,还需要绘制详细的截面图和三维模型,标注出各个部分的尺寸和角度。
材质要求:根据使用环境和功能要求确定铝型材的材质。常见的铝合金有6061、6063、6005等,不同牌号的铝合金在强度、硬度、耐腐蚀性等方面有所差异。例如,6061铝合金具有良好的强度和耐腐蚀性,适用于制造建筑结构部件;6063铝合金具有良好的挤压性能和表面光洁度,常用于制造外观要求较高的装饰型材。
表面处理:确定是否需要对铝型材进行表面处理,以及所需的表面处理方式。常见的表面处理方式有阳极氧化、电泳涂漆、粉末喷涂、氟碳漆喷涂等。阳极氧化可使型材表面形成一层致密的氧化膜,提高耐腐蚀性和硬度;电泳涂漆能使型材获得均匀、光滑的表面涂层,且颜色鲜艳;粉末喷涂可以提供丰富的色彩选择,同时具有较好的耐磨性和耐腐蚀性;氟碳漆喷涂则具有优异的耐候性和抗老化性能,适用于户外环境。
模具设计
设计工具:使用专业的CAD(计算机辅助设计)软件,如SolidWorks、UG NX、Pro/E等进行模具设计。这些软件可以精确地绘制模具的三维图形,并进行模拟分析和优化。
模芯和模膛设计:根据铝型材的截面形状和尺寸,设计模芯和模膛的结构。模芯是形成铝型材内部形状的关键部件,模膛则决定了铝型材的外部轮廓。确保模芯和模膛的尺寸精度和表面粗糙度符合要求,以保证挤出的铝型材尺寸准确、表面光滑。
分流孔和工作带设计:合理设计分流孔的位置、大小和形状,使铝液在模膛内能够均匀分布。工作带的设计直接影响铝型材的挤出速度和尺寸精度,要根据铝型材的形状和尺寸进行优化,确保各个部位的金属流量均匀一致。
模具材料选择:模具通常采用高强度、耐高温的模具钢制造,如H13钢、SKD61钢等。这些钢材具有良好的热稳定性和耐磨性,能够承受铝液的高压和高温冲击。
模具加工
CNC加工中心:将设计好的模具图纸导入CNC(计算机数字控制)加工中心,由加工中心自动完成模具的粗加工和精加工。CNC加工可以保证模具的尺寸精度和形状精度,加工效率高。
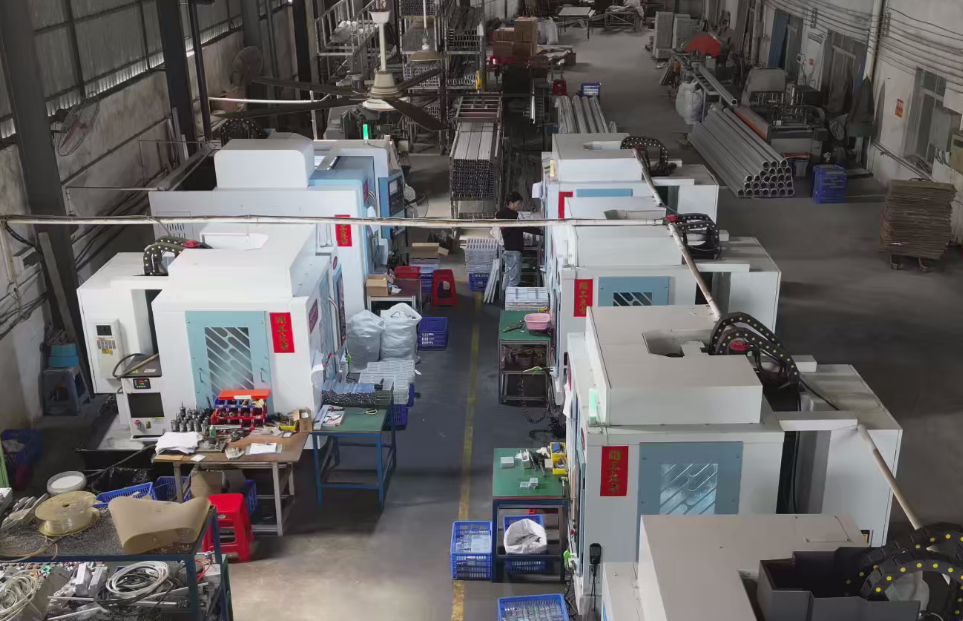
火花机加工:对于一些形状复杂、精度要求高的模具部件,如模芯上的细小孔、棱角等,采用火花机进行加工。火花机利用电极与工件之间的火花放电腐蚀原理,去除金属材料,实现高精度的加工。
线切割加工:线切割主要用于加工模具中的窄缝、尖角等部位。通过钼丝或铜丝的放电切割,能够获得精细的加工效果,保证模具的精度和质量。
手工打磨和抛光:在模具加工完成后,需要进行手工打磨和抛光,去除加工过程中留下的刀痕、毛刺等缺陷,使模具表面光滑、平整,提高模具的质量和使用寿命。